Cross dock efficiency comes with technology and touchpoints
Delivering freight from Point A to Point B is challenging at the best of times, but it can be evermore complex when cargo needs to be shifted from one trailer to another.
It’s why efficient cross-dock operations are so critical to less-than-truckload fleets.
Operating the cross dock itself is simple as long as a carrier can ensure fluid operations, says Brett Poe, a member of the Apex Motor Express logistics team. And he believes the secret to that is to reduce the number of touchpoints during the delivery process.
“[Make sure] everything keeps moving, and nothing sits too long,” Poe says. “If you’re touching something more than once, it’s costing you time and money.”
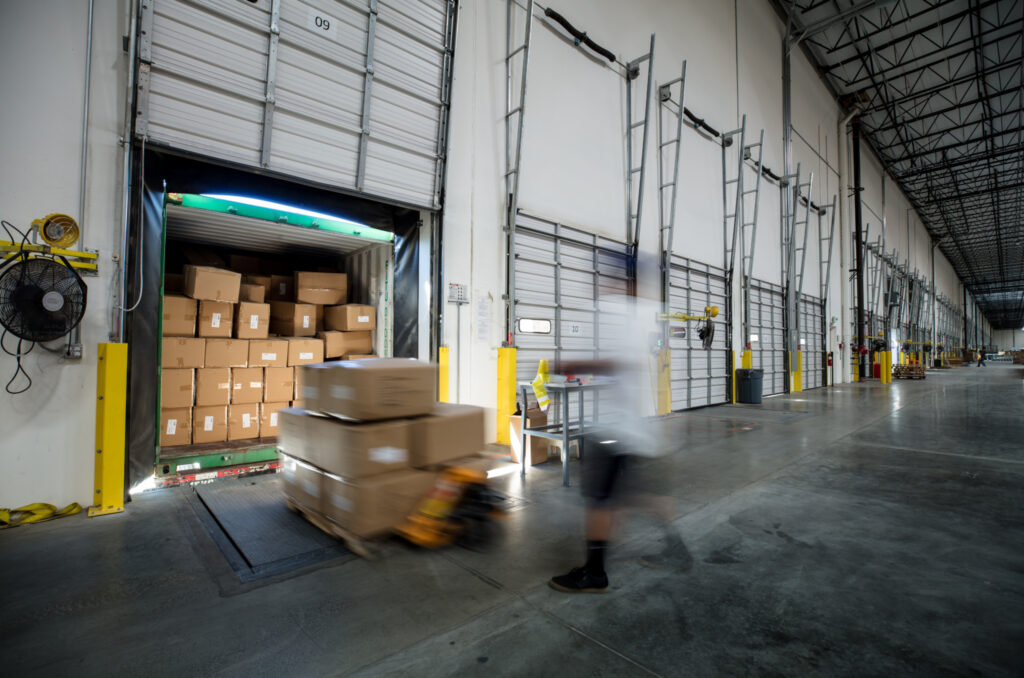
Paperless processes
Delays and disruptions can be linked to something as simple as errors with paperwork entries – one of the reasons some operations are shifting to paperless systems and auto-populated data fields.
At Van Kam Freightways, for example, everything’s traced by electronic manifests, and tablets are used on the docks, says Kevin Highfield, regional manager for the British Columbia interior.
But the data is only part of the equation. Ensuring a proper place for every piece of freight also plays a role in ensuring nothing is misplaced and routings remain correct.
“Every time we move a piece of freight, we give that freight a home so we know exactly where it is,” he adds.
Knowing those locations will save a lot of time on a cross dock.
“When we pick up freight from our shipper, we have the ability to take a picture of that freight electronically and send that bill to the billing system,” he says, adding that this allows shipments to be tracked in real time. Such visibility helps stay informed about the location and status of freight at any given moment throughout the day.
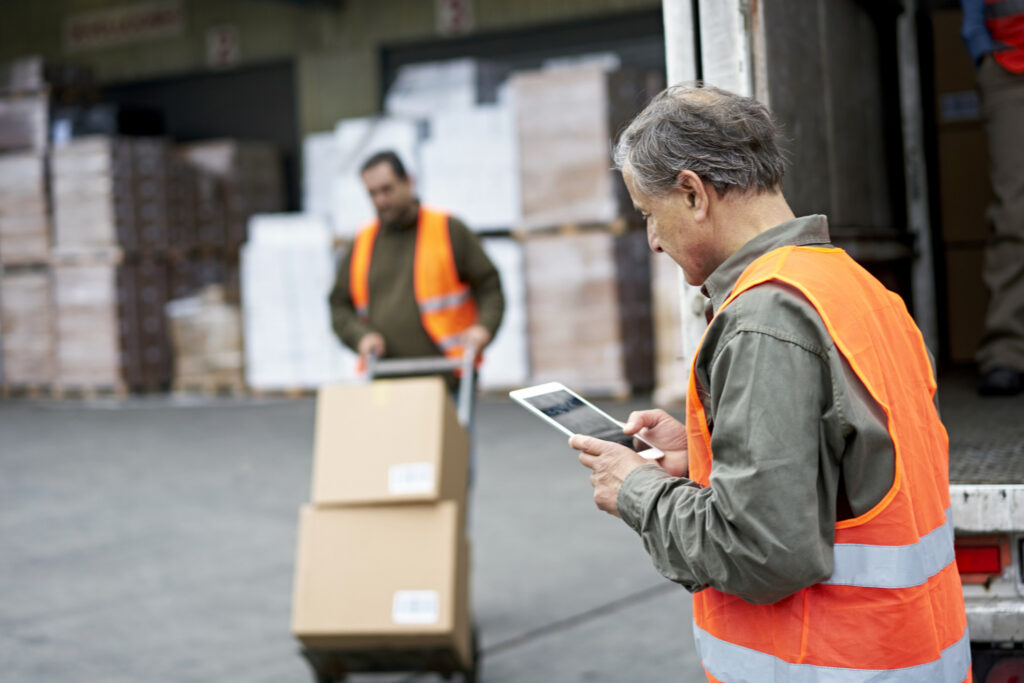
Technologies and touchpoints
Van Kam has also divided its freight handling into three categories: overnight freight, priority freight with guaranteed delivery by noon, and regular freight that can be delivered by 5 pm the next day. An AS 400 system and tablets are used to track this. Each type of freight is color-coded on the tablet interface, and specific trailers are allocated different types of freight to maximize productivity, Highfield says.
Marc Murdoch, senior director of transportation at Polaris Transportation Group, says his fleet combines different technologies and sorting systems. For example, the dock has different lane setups based on destinations. Scanning guns are used to receive information about packages as they’re unloaded. From there, the goods go to a designated side of the dock where they will be waiting to be loaded onto an outbound trailer.
“It looks like a trailer is being built on the dock. And as soon as our customs team gives us the green light, the lane is good to go. Then we will disperse that lane, and this trailer that we’ve been essentially building on the dock is now just going to get loaded up,” Murdoch says.
Software and hardware track cargo along a route, and even sends alerts when the trailer doors are open.
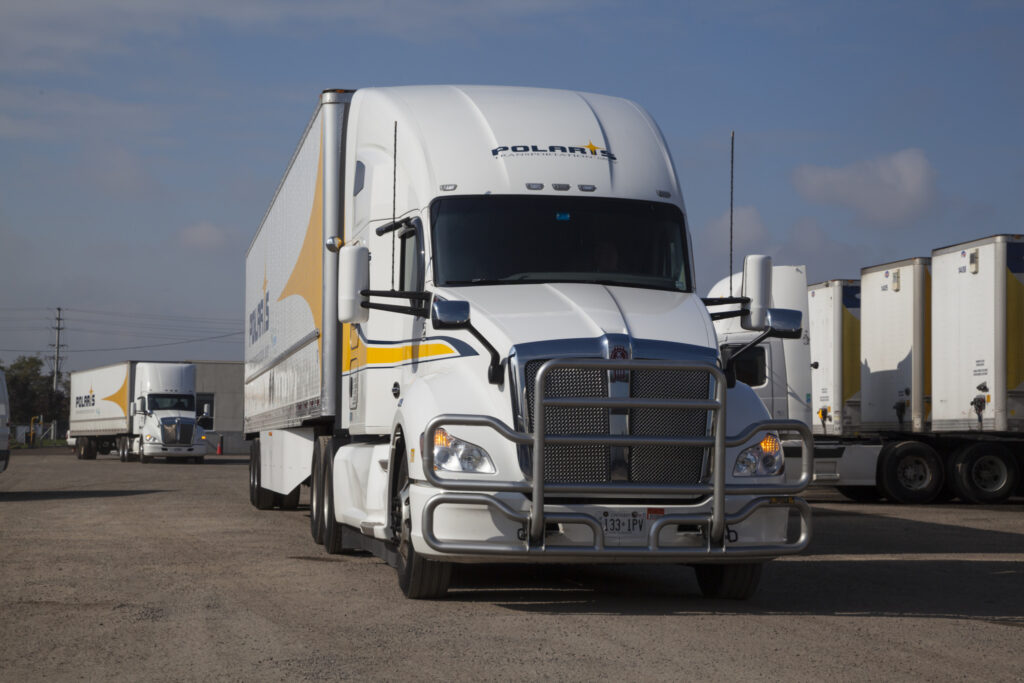
Extra touchpoints
However, despite all the perks technology has to offer, sometimes it can add extra touchpoints to the operations, Poe warns.
“If you’ve got something that’s got to be scanned at every single location that it crosses or goes through, that’s an extra touch point on something.” Backup systems can serve as an extra touchpoint when other technologies fail.
Murdoch believes in efficient planning, too. Understanding the math behind the operations is essential to ensure there are enough people and equipment on the dock to handle the freight volumes, he says.
One of his first tasks after joining Polaris last October was to determine how efficiently freight moved in and out of the dock. Tracking the number of scans for incoming and outgoing shipments was the way to do it, making it possible to calculate how much freight could be processed per shift. From there, it was easy to understand the required man hours and timeframes for different tasks, Murdoch says.
When it comes to tasks on the cross dock, the appropriate tools and equipment are important as well, he says. This includes not just forklifts, but also tools like hammers, crowbars, and materials that can be used to secure the goods and prepare them for loading.
Not all pieces of freight are ready to go onto trailers as is.
“You might need to have a certain set of forklifts with six-foot blades on them, instead of four-foot blades or five-foot blades,” he says. “Having that stuff available for the team, teaching them how to use it properly and keeping it maintained, is critical.”
Additional skills needed
The team will also need to draw on a wide range of skills, he adds.
Even though everyone has individual tasks and assignments, the day’s business needs might require them to step up in a different operation.
“We might get five or six unloads that show up here at eight o’clock in the morning. That’s catastrophic because I have 60 drivers that are waiting to go. So, we would have to decide quickly.”
Highfield points to last year’s flood-related road closures in B.C. as an example of unforeseen crises that require decisions to be made on the go. The fleet kept picking up freight, expecting the roads to be reopened at any time, but eventually ran out of equipment. It took some time to catch up with the freight flows once roads reopened.
“I think if we were going to do that in the future, we would definitely take some time. We tried to be heroes,” he says.
Have your say
This is a moderated forum. Comments will no longer be published unless they are accompanied by a first and last name and a verifiable email address. (Today's Trucking will not publish or share the email address.) Profane language and content deemed to be libelous, racist, or threatening in nature will not be published under any circumstances.