Dragging brakes sacrifice more than friction material
An object like a tractor-trailer remains in motion unless an outside force like the braking system acts upon it. Even Isaac Newton could have predicted that. And when brake components fail, there’s always a worry the truck won’t stop in time.
But the consequences of brake-related failures are not limited to the sound of a resounding crunch. Dragging brakes, which don’t release when they should, can sacrifice fuel economy, scrub away valuable tire treads, and render otherwise-useful friction material to dust.
According to Bendix calculations, a tractor-trailer will consume 1.5% more fuel if its brakes drag just 25% of the time.
“Once you have a dragging brake, the only way to resolve it is to either burn through the friction to the point where the drag becomes insignificant, or have a technician identify it and manually adjust the brake,” Mark Holley, Bendix director of marketing and customer solutions – wheel ends, noted in a related bulletin.
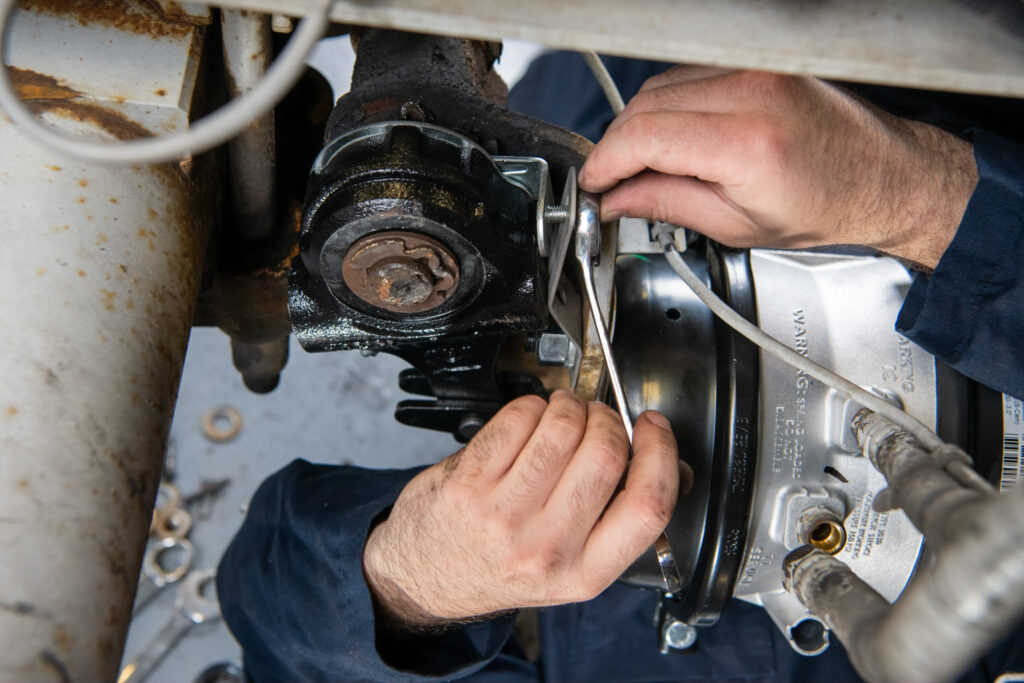
Brake adjustment problems
In many cases, the problem can be traced to well-intentioned personnel who over-adjust their brakes, says Eric Coffman, Cummins-Meritor senior manager – independent product strategy. “With an automatic slack adjuster, you really don’t need to be adjusting brakes, but people kind of still want to … Maybe they’re close to that [prescribed] limit for stroke or feel like, ‘Hey, my stroke’s over. I can adjust this and get back into compliance.’”
Technicians or drivers who adjust a clearance-sensing slack adjuster actually cause clutches to slip and components to wear prematurely. “Somebody who thinks they’re doing right by adjusting it, they’re actually slowly killing this fairly expensive foundation brake component,” he says.
The true cause of the problem is more likely a worn or failing component like a camshaft, cam bushing, or slack adjuster – or combination thereof. (“If you have a worn camshaft, you probably have a worn bushing. They’re mating components that go together.”)
Such underlying issues can be overlooked if technicians simply slap a new shoe in place and send equipment on its way.
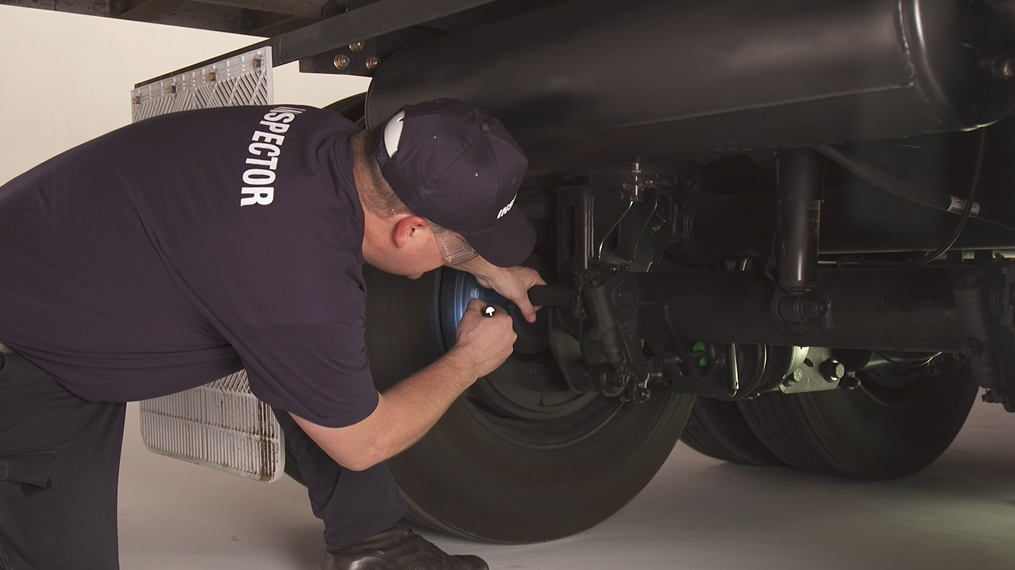
Failure by design
But the challenge of dragging brakes can also be traced to the way an automatic slack adjuster (ASA) is designed, says Frank Gilboy, Bendix product group director – drum brake, slack adjuster, and wheel end products.
“When you get a drum brake hot and the drum brake expands, a slack adjuster does exactly what it’s supposed to do,” he says. “It starts adjusting to that expanded hot brake [drum]. What happens then, of course, is the brake cools down and returns to that original dimension.”
While one model might adjust a quarter inch after 12 brake applications, another can wait 45 applications before making the same adjustment. “They’re still doing what they’re supposed to be doing,” Gilboy says. The model that is quicker to chase after a temporarily expanding brake drum is simply more likely to expose the friction material to some added contact.
The model of slack adjuster that waits a little longer before adjusting will maintain the all-important running clearance between the drum and friction material — extending lining life by 16% and drum life by up to 30%, Holley says, citing third-party research conducted for Bendix.
Yes, the unwanted contact can wear down more than the friction material alone.
Resins baked into the friction material deposit on a brake drum’s surface. “When you start to burn out those resins, now you no longer have that really well-maintained layer between the two, and the friction doesn’t work the way it’s supposed to,” Gilboy says. “That resin is gone, and now you just have more of the abrasives in there – and those abrasives tend to dig in and wear the drum more than they [otherwise] would.”
The damage accelerates.
Unwanted heat
Higher wheel end temperatures that come with the added friction will compound matters, accelerating how quickly the friction material wears away, Coffman says. And such temperatures climb high enough, they could even trigger a thermal event, he adds.
In other words, they could trigger a wheel fire.
“There’s components in the material that are flammable at a certain temperature,” he says. “If you get a bunch of oil on a red-hot metal surface, that’s going to catch on fire more easily.”
Gilboy isn’t convinced. While dragging brakes also generate extra heat, he says the temperatures won’t climb high enough to ignite the wheel end fires associated with issues like seized wheel bearings. “The brake essentially becomes ‘self-clearancing,’… It only drags for so long before it wears the friction away.”
Once a typical trip is complete, brake temperatures across the vehicle should be within 50 Fahrenheit of one another, Coffman says, referring to something shops can monitor with a laser thermometer. “If you had a brake that’s wildly hotter than the other, that’s a pretty quick check to know that you’ve got some type of foundation brake issue and need to investigate.”
Any lack of running clearance between the friction material and drum is another obvious sign of trouble, Holley says. And wheels should turn freely when the truck is on a lift.
Technicians should always detect some amount of free play unless the slack is running hard against the drum, Gilboy adds, noting that every brake manufacturer or slack manufacturer will prescribe just how much free play should exist.
No matter what the cause, however, drivers are unlikely to spot the issues. Engines will easily power through the unwanted grip of a single dragging brake. At best, drivers might spot broken hardware or a lack of running clearance during a visual inspection.
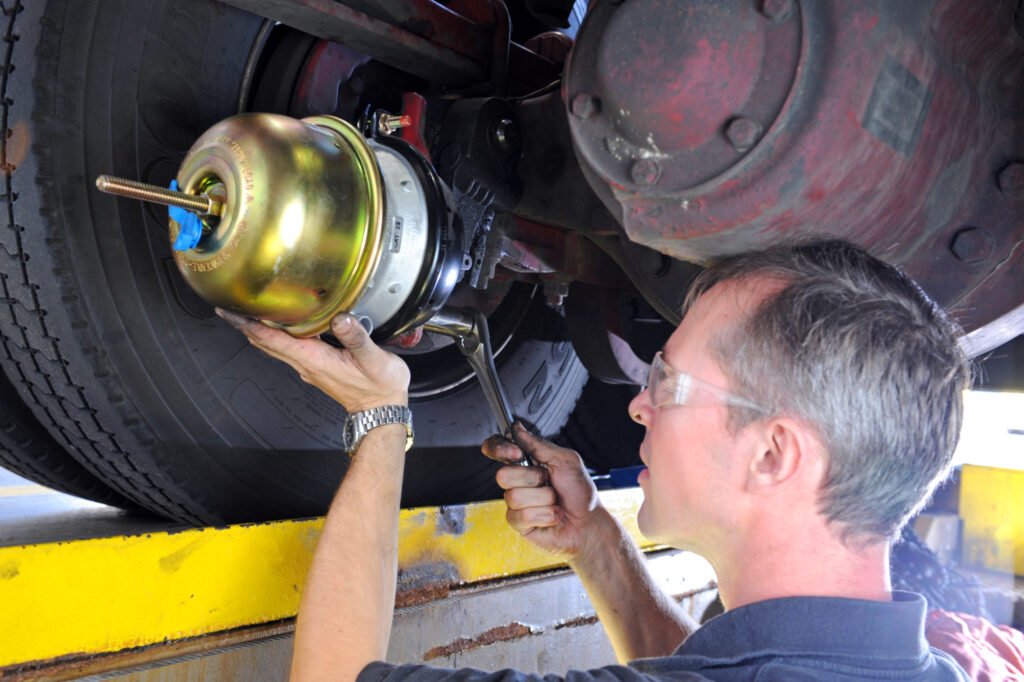
Brake chambers
Failing brake chambers can be another underlying source of trouble. Sealed and coated spring brakes are marketed because corrosion can be such a problem, Coffman says.
The American Trucking Associations’ Technology and Maintenance Council (TMC) recommends replacing service or spring brake chambers that show significant signs of corrosion, such as holes that penetrate the housing.
Drain holes should also be cleared to allow moisture to escape – a particular issue for trucks that travel through debris-laden environments like construction sites, or bottom-dump trailers.
Picking friction
Once related parts are addressed, the choices in replacement friction material will determine how quickly the truck comes back to the shop. And Coffman says there will always be trade-offs to consider.
“You get quiet. You get good stopping power. You get amazing wear. And you get price. And you kind of get to pick from those,” he explains.
Some buyers emphasize the total cost of ownership, while others focus more on initial purchase prices. Applications make a difference as well. A tractor-trailer that hauls packing peanuts across Kansas will have different needs than a garbage truck that stops every 120 feet, 12 hours a day, six days a week, Coffman says.
“There’s stuff that wears really well at 250 degrees but might not do great at 550 degrees.”
Have your say
This is a moderated forum. Comments will no longer be published unless they are accompanied by a first and last name and a verifiable email address. (Today's Trucking will not publish or share the email address.) Profane language and content deemed to be libelous, racist, or threatening in nature will not be published under any circumstances.
Quote from this article: “Once you have a dragging brake, the only way to resolve it is to either burn through the friction to the point where the drag becomes insignificant, or have a technician identify it and manually adjust the brake,” Mark Holley, Bendix director of marketing and customer solutions – wheel ends, noted in a related bulletin.”….sorry, but there is one more way, that can lead to resolving a dragging brake before it becomes an issue: Driver input!
If drivers were to perform their periodic circle-checks in more than a perfunctory way, their finger-tips would notice a hot-running brake-drum, and thus could get the brake checked by a mechanic before the end of the shift (and, probably avoid an Inspection-Station OOS defect in the process).
Very interesting article on truck brakes, thank you for publishing this. We manufacture industrial brakes for various applications which are typically larger than standard vehicle brakes, but the engineering and physics is the same of course. This was a nice overview of issues we all face when designing brakes even though it is more geared towards maintenance, again, much appreciated.