Daimler SuperTruck II showcases the future of freight efficiency
A handle like “SuperTruck” is hard to live up to — let alone twice. But Daimler Truck North America has unveiled its latest contribution to a U.S. Department of Energy program designed to spur innovations in the name of freight efficiency.
SuperTruck II showcases an array of enhancements, from updated tractor aerodynamics to low-rolling-resistance tires, powertrain improvements, and innovative energy management systems. And the end result is the most aerodynamic truck ever to wear a Freightliner nameplate.
The latest truck doubles the freight efficiency of the baseline 2009 Freightliner Cascadia and DD15 engine that achieved 6 miles per gallon (39.2 L/100 km), and even betters a previous prototype known as SuperTruck I.
“Taken all together, the combined innovations developed for the Freightliner SuperTruck II have provided us the opportunity to explore the technologies needed to meet stringent and forthcoming Greenhouse Gas reduction requirements in the coming years,” said Rainer Muller-Finkeldei, senior vice-president – engineering and technology.
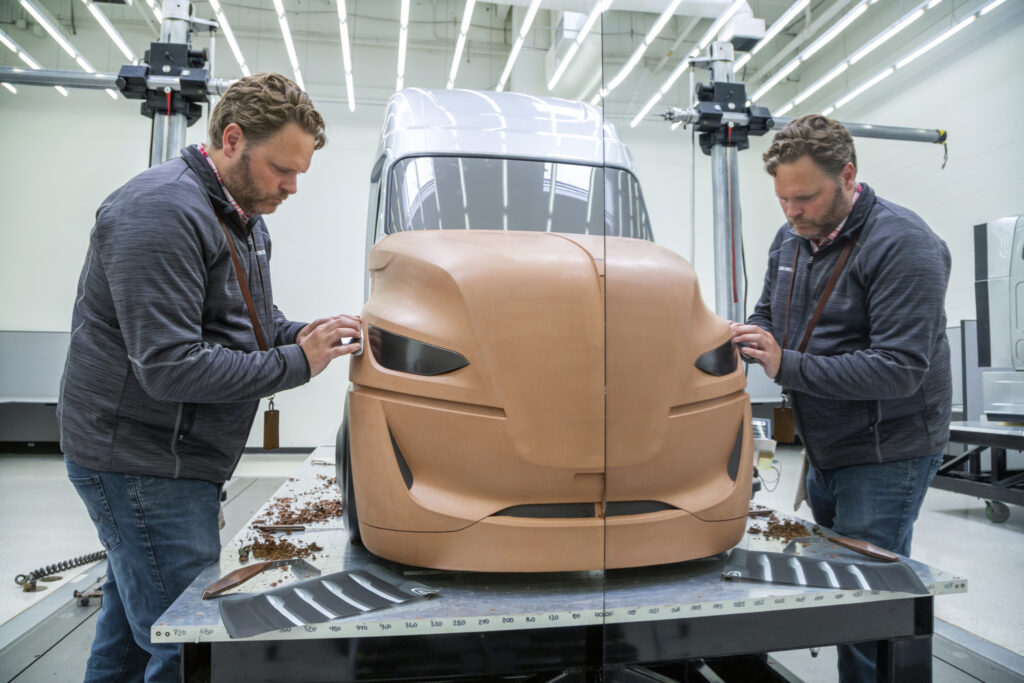
Aerodynamic enhancements
The shape alone represents a significant shift.
“When the viewer sees it, they can see the efficiency,” chief designer Jeff Cotner said, referring to the truck’s sculpted lines. The grille is recessed rather than sitting on the surface, the bumper tucks under the air duct, and the bottom of the doors and chassis fairing form a blended surface.
All together, the changes better the aerodynamic drag of SuperTruck I by 12%.
“We’ve got something here that is actually awesome from an aerodynamic standpoint, but also I think makes a very beautiful truck.”
Engineers further enhanced the shape by incorporating active side extenders and a roof spoiler system that will automatically tighten the gap between the tractor and trailer to a mere four inches at highway speeds. And a dynamic height control drops the bottom of the tractor-trailer to within inches of the highway surface.
Think Nascar-like approaches, but with a tractor-trailer.
Further gains are realized by removing West Coast mirrors and replacing them with a mirrorless camera system, which is allowed under an exemption from the U.S. National Highway Traffic Safety Administration. This has shown promise in enhancing visibility as well, and Daimler Truck says that helps to make the business case for regulatory changes to permit widespread adoption.
Powertrains and EcoSailing
Under the hood, a prototype 13-liter Detroit engine is linked to a 13-speed overdrive transmission, rather than the 10.7-liter engine and Detroit DT12 transmission featured in SuperTruck I.
These combine with various powertrain enhancements including an EcoSail feature that shuts down the engine and allows the truck to coast under select conditions, a split cooling system with high- and low-temperature cooling circuits, and smart engine lubrication circuit to reduce fuel consumption by 5.7% when compared to the previous prototype.
“The intent is to really optimize where the high-power, high-efficiency of the engine is,” said manager – advanced vehicle systems Darek Villeneuve, referring as well to SuperTruck II’s 1.75 rear axle ratio. Highway speeds that might typically see an engine turn at 1,100 rpm are now achieved at 950 rpm.
“We were able to make a significant efficiency improvement on the combustion and the air handling system,” he added, noting that parasitic loads are reduced through features like the battery-electric air conditioning and power steering systems.
And the split cooling system enhances the two-stage turbocharging and exhaust gas recirculation cooling, allowing for aggressive downspeeding. A new lubrication circuit minimizes pumping losses by dividing flows to the most sensitive components as well.
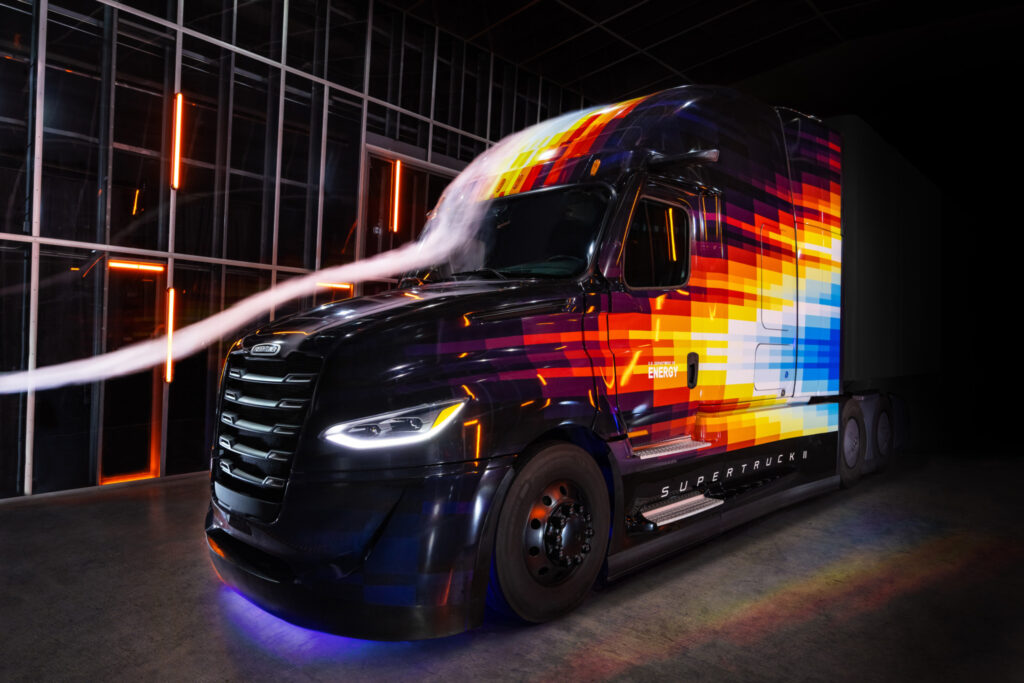
Adaptive axles and tires
At the rear of the tractor, adaptive tandem axles will shift from a 6×4 configuration to a fuel-efficient 6×2 at highway speeds.
The prototype steer tires and dual drive and tag axle tires were developed alongside Michelin, helping reduce tractor rolling resistance compared to SuperTruck I’s wide-base tires. And dynamic load shifting will automatically shift loads from the drive axle to the tag axle to maximize the tag tire’s low rolling resistance.
Together they reduce tractor rolling resistance by 12%.
“This tire set is designed for that 6×2 highway where all your torque is going through the drive axle,” Villeneuve added. “We not only lowered the rolling resistance of that drive axle, we improved the wear resistance by over 20% on that tire.”
48-volt electrical system
While this isn’t a battery-electric truck, SuperTruck II features a 48-volt electrical system and lithium-ion batteries. They support a new electric steering system that adjusts demand at low speeds or highway speeds, an electric air conditioner that runs when the engine itself is shut down in the EcoSail mode, and the 12-volt power needed for standard offerings such as lighting and the cab’s instrument cluster.
Typical power steering systems are designed for low speeds and need a large boost, leading to components that are essentially overdesigned for highway speeds.
“With this system we’re able to control it such where we can run [a] high-rpm pump speed, and get unbelievable easy steering at low speed. And when you’re going on the highway you don’t need a lot of boost and we drive all that power back, so therefore you’re not consuming extra energy that you don’t need,” Villeneuve said, explaining the benefits.
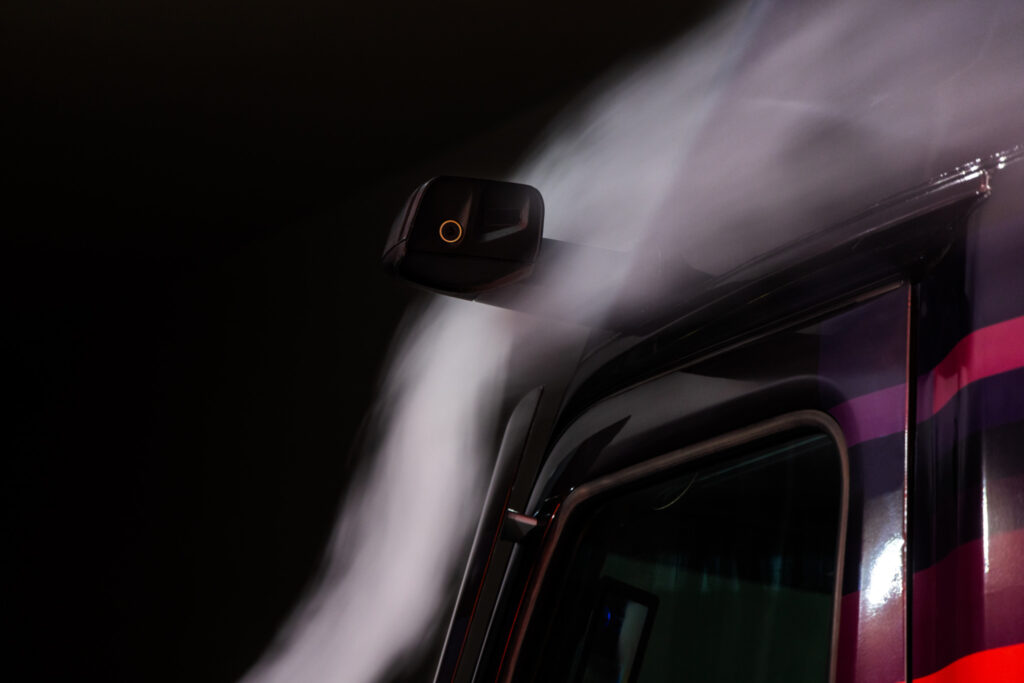
EcoSailing away
One of the vehicle’s most radical features comes in the EcoSail mode that captures the power of momentum.
“Imagine you’re driving a truck, you’re going down a hill, and then what happens is the engine actually shuts off. So you’re ‘sailing’ and it’s extremely quiet,” Villeneuve said. “There’s times on certain routes you’re sailing for quite a long time. And the vehicle understands that if you’re going down a hill and you need to do engine braking, you put [the engine] back on. Or if you start going too slow, to maintain the speed, it comes back on automatically.”
While some of the features are decidedly futuristic, several innovations on the first SuperTruck have found a home in the Freightliner Cascadia, from aerodynamics enhancements to improved engine thermal efficiency, downspeeding, the windshield, and predictive powertrain controls.
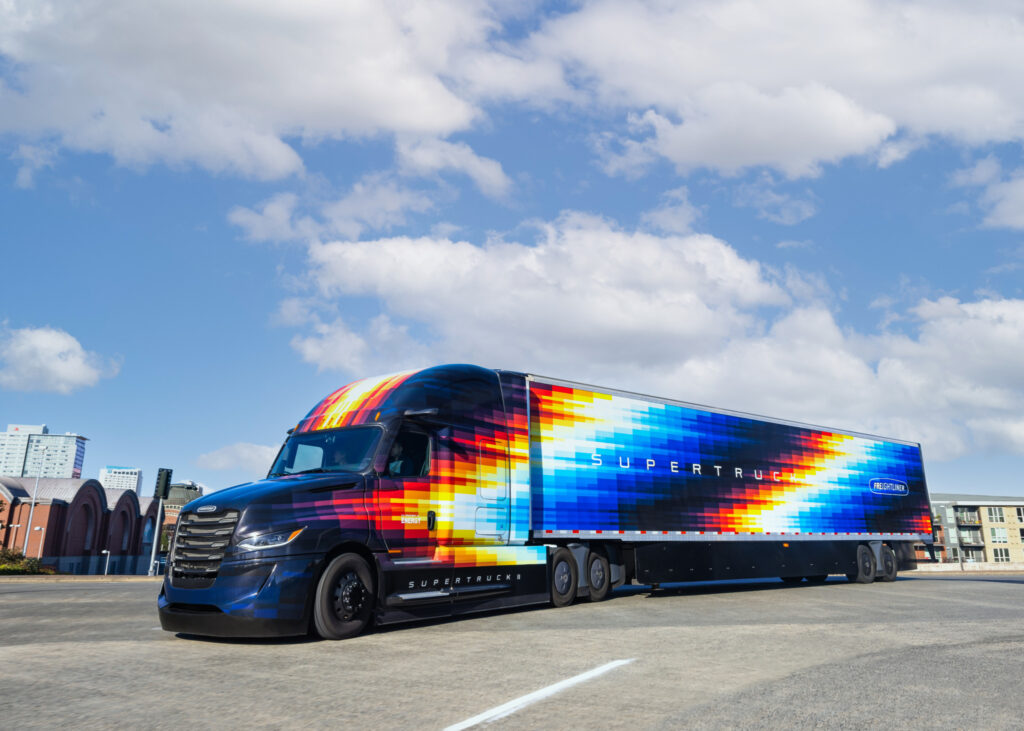
But other SuperTruck I features were left behind for specific reasons, such as a prototype waste heat recovery system.
“It turned out it was a very large, heavy and expensive system that was not really able to capture as much energy as we’d hoped,” said Derek Rotz, director – advanced engineering. “It worked OK in a laboratory setting, but in the real world when your engine’s revving up and revving down, the system wouldn’t work very well.”
That system also limited SuperTruck I’s optimal hood shape and engine compartment layout. Eliminating it gave engineering teams more flexibility when working on SuperTruck II.
SuperTruck I’s high-voltage hybrid systems were also abandoned along with pricey carbon fiber materials and extreme trailer dynamics that affected payloads.
This time, the work represents a smaller leap to real-world applications.
Looking beyond diesel
The collective features in SuperTruck II will support more than future diesel-powered equipment alone. Aerodynamic enhancements and lower tire rolling resistance also apply to fuel-cell-electric vehicles, Rotz noted.
Those hydrogen-powered systems are playing a central role in the SuperTruck III project that has been underway for a year, drawing on US$25.79 million in funding to create a pair of Class 8 trucks with a 965-km range, 25,000 hours of durability, and a payload that matches diesel-powered equipment by 2027.
“Fuel cells is a fundamentally different vehicle and we’re actually learning a lot,” Rotz said of the work so far.
It’s part of US$199 million in funding for 25 projects from various OEMs that will develop trucks powered by batteries and fuel cells, along with the related charging infrastructure.
The various technologies that emerge on the journey to zero-emission vehicles will not all come at once, Rotz observed. “We are going to introduce these technologies at the right pace … and do them also for the right reasons.”
While Daimler Truck has committed to be carbon-neutral by 2039, there is still a lot of work to be done before that goal is achieved, he added.
“For the next few years to come, diesel will still be part of our portfolio,” Rotz stressed. “Projects like SuperTruck II enable us to help move the needle on those technologies.”
Have your say
This is a moderated forum. Comments will no longer be published unless they are accompanied by a first and last name and a verifiable email address. (Today's Trucking will not publish or share the email address.) Profane language and content deemed to be libelous, racist, or threatening in nature will not be published under any circumstances.